Compressed Air System Overview
Compressed air is often referred to as the "fourth utility" in manufacturing, standing alongside electricity, water, and natural gas in terms of its critical importance. Found in virtually every industrial facility, compressed air systems provide a versatile, reliable, and efficient source of power for a wide range of manufacturing processes. From pneumatic tools and material handling to instrumentation and process control, compressed air plays a vital role in ensuring smooth and efficient operations.
Despite its widespread use, compressed air is also one of the most expensive utilities, with inefficiencies leading to significant energy waste and higher operational costs. A well-designed and properly maintained compressed air system can enhance productivity, improve product quality, and reduce energy consumption, making it a key focus area for manufacturers looking to optimize efficiency and sustainability.
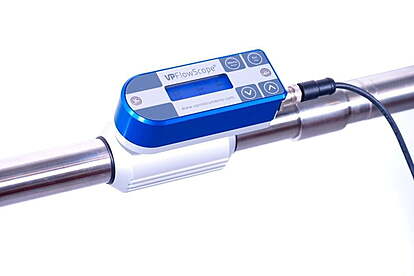
Inline Compressed Air Meters
Pros and Cons of Inline Compressed Air Meters
✅ Pros:
- Real-Time Monitoring – Provides continuous data on air flow and pressure, allowing for instant detection of inefficiencies.
- Leak Detection – Helps identify and quantify leaks, reducing unnecessary air loss and lowering energy costs.
- Energy Efficiency Optimization – Enables businesses to optimize compressor operation based on actual air demand.
- Accurate Consumption Measurement – Essential for cost allocation and billing in multi-department or multi-user facilities.
- Improves System Reliability – Ensures stable pressure levels and prevents overloading of compressors.
- Supports Predictive Maintenance – Data from inline meters can be used to schedule maintenance before failures occur.
❌ Cons:
- Initial Installation Cost – Purchasing and installing inline meters can be expensive, especially for large systems.
- Potential Pressure Drop – Some meter designs can introduce minor pressure losses, impacting system performance.
- Calibration and Maintenance Required – Over time, sensors may drift and require recalibration to maintain accuracy.
- Not Always Suitable for Low Flow Applications – Some inline meters may struggle to accurately measure very low air flows.
- Sensitivity to Contaminants – Dust, oil, and moisture in compressed air can affect sensor accuracy and lifespan.
Inline compressed air meters play a crucial role in improving efficiency, reducing costs, and optimizing system performance in industrial settings. While they offer accurate monitoring, leak detection, and energy savings, factors like cost, maintenance, and installation complexity should be carefully considered when integrating them into a compressed air system. Choosing the right meter based on system size, flow rate, and environmental conditions will ensure maximum benefits and long-term operational success.
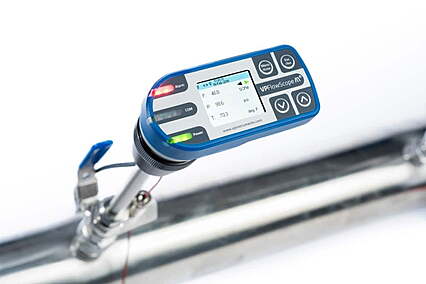
Insertion Thermal Mass Compressed Air Meters
Pros and Cons of Insertion Thermal Mass Compressed Air Meters
✅ Pros:
Non-Intrusive Installation – Can be installed without significant modifications to the piping system, reducing downtime.
Suitable for Large Pipes – Works well in large-diameter pipelines where inline meters may not be practical.
Accurate Mass Flow Measurement – Directly measures mass flow rather than volumetric flow, eliminating the need for pressure and temperature compensation.
Energy Efficiency Monitoring – Helps facilities track compressed air usage, identify inefficiencies, and improve overall energy management.
Low Pressure Drop – Minimal disruption to airflow, ensuring efficient operation.
Cost-Effective for Retrofits – Ideal for adding monitoring capabilities to existing compressed air systems without requiring major system changes.
❌ Cons:
Requires Proper Installation – Accurate measurements depend on correct sensor placement and adequate straight pipe runs.
Not Ideal for Rapidly Changing Flow Conditions – Response time may be slower than some other flow measurement technologies.
Sensitive to Dirt and Moisture – Contaminants in the air can affect sensor accuracy and longevity.
Initial Calibration and Maintenance Needed – Regular calibration is necessary to maintain long-term accuracy.
Limited Suitability for Very Low Flow Rates – May struggle with measuring very low air velocities effectively.
Conclusion
Insertion thermal mass compressed air meters are an effective solution for monitoring large-scale compressed air systems with minimal installation disruption. Their ability to measure mass flow directly, combined with low pressure drop and cost-effective installation, makes them a popular choice in industrial applications. However, careful installation, calibration, and maintenance are necessary to ensure reliable and accurate performance. Choosing the right meter based on system requirements will maximize efficiency and energy savings.
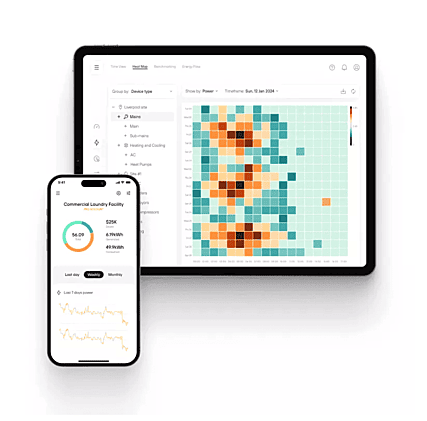
Data Integration and Dashboarding
Energy monitoring was never this easy with our cloud based monitoring solutions. View your compressed air system from anywhere in the world, and involve experts when needed. Your service provider can now have a first look and analyze your measurement data without coming to your factory, e.g. in case of issues or for advice on system improvements and energy savings.
Integrate system pressure, temperature and flow data from the installed meters into the cloud dashboard for easy data management.
We believe that all metered compressed air flow, pressure, temperature, compressor cycling data should always be integrated to either a site or cloud based SCADA to provide optimal data access and value to the facility. A non-integrated metering system has limited value since access to the meters are typically challenging and requires someone to physically read their data. These spot checks provide no guidance or visibility on the system's operations the many other minutes / hours of the day. Once integrated, data is stored and can be retrieved with ease for analysis and performance checks.