Industrial Solutions
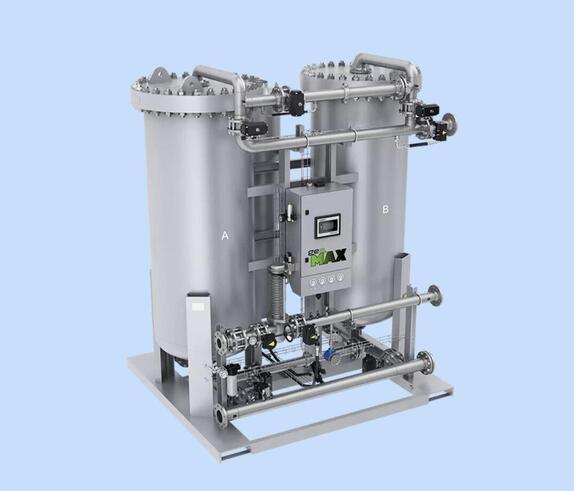
Onsite Nitrogen N2 and Oxygen O2 Generation
Onsite Nitrogen N2 and Oxygen O2 Generation
Harnessing the Power of Compressed Air:
With the increasing demand for nitrogen across various industries, the traditional reliance on delivered liquid nitrogen or cylinders is being replaced by more efficient and cost-effective methods. Our advanced technology harnesses the power of compressed air to produce high-purity nitrogen directly at your facility, offering unparalleled convenience and reliability.
What is Onsite Nitrogen Generation?
Onsite nitrogen generation is the process of producing nitrogen gas directly at the point of use, eliminating the need for storage, transportation, and delivery of nitrogen cylinders or liquid nitrogen. This is achieved through the separation of nitrogen molecules from compressed air, utilizing advanced membrane or pressure swing adsorption (PSA) technology.
Benefits of Onsite Nitrogen Generation:
Cost Savings: By generating nitrogen on-site, businesses can significantly reduce their nitrogen expenses compared to purchasing nitrogen cylinders or liquid nitrogen. This results in lower operational costs and improved overall profitability.
Convenience and Accessibility: Onsite nitrogen generation provides businesses with immediate access to nitrogen whenever and wherever it is needed, eliminating the inconvenience of waiting for deliveries or managing cylinder exchanges.
Continuous Supply: Unlike traditional nitrogen delivery methods, which are subject to supply chain disruptions, onsite nitrogen generation ensures a continuous and reliable supply of nitrogen, even during peak demand periods.
High Purity: Our onsite nitrogen generation systems produce nitrogen gas with purity levels tailored to meet the specific requirements of your application, ensuring optimal performance and quality consistency.
Environmental Sustainability: Onsite nitrogen generation reduces the carbon footprint associated with transporting nitrogen cylinders or liquid nitrogen, contributing to environmental sustainability and corporate responsibility initiatives.
Why Choose EES for Onsite Nitrogen Generation?
Expertise: With years of experience in the nitrogen generation industry, [Your Company Name] possesses the knowledge and expertise to design and implement customized onsite nitrogen generation solutions for a wide range of applications.
Advanced Technology: We leverage state-of-the-art membrane and PSA technology to deliver efficient and reliable onsite nitrogen generation systems that meet the highest standards of performance and reliability.
Tailored Solutions: We understand that every business has unique requirements. That's why we work closely with our clients to design customized onsite nitrogen generation solutions that address their specific needs and challenges.
Comprehensive Support: From initial consultation and system design to installation, training, and ongoing maintenance, [Your Company Name] provides comprehensive support every step of the way, ensuring the success of your onsite nitrogen generation project.
- Cost of electricity - The site's cost of electricity has to be low enough to minimize the cost per CFM of compressed air. From our experience, a fully loaded (cost of generation and transmission) should be at most $0.15 / kWh. This rate structure will provide some operational buffer to the project to account for system inefficiencies and long term service costs for the nitrogen generation equipment.
- Ideally, an oil free compressed air system - This is not essential but a preference. Oil filled compressors introduce a contaminant into the compressed air supply that if untreated or not well managed can foul the nitrogen generation system. From our experience, no matter how well run an oil filled system is, there will always be a possibility of a system failure that will lead to either water and / oil being introduced into the central air header and subsequently into the nitrogen generators. We recommend proper dew point monitoring, buffer tanks with automatic drains be installed into these systems to reduce the risk of fouling the nitrogen generators.
- A contract price for bulk liquid nitrogen that is sufficiently high enough to provide savings to the facility to convert to self-generated nitrogen. This price barrier or difference will depend on the specific payback or ROI needed by the facility to justify productivity projects. This is an important factor in developing a project that will achieve the necessary payback period to obtain the necessary funding.
- A nitrogen purity level that is at the 99.5% nitrogen purity. The nitrogen generator reduces in output efficiency at high purity values. As the desired nitrogen purity approaches 99.99%, the amount of compressed air lost to purges will increase, which increases the energy burden on the system to generate the needed air to service the nitrogen generator for system purges. At the same time, the higher the purity value, the lower the nitrogen generator's output capacity. Each nitrogen generation system will have its own rated output based on the purity setpoint of the generator.
- A compressed air system pressure that is high enough to generate the nitrogen at the required system pressure. Various nitrogen blenders or injection systems require nitrogen at certain pressures. From our experience, the pressure drop needed to achieve optimal nitrogen flow through a generator is roughly 30 PSIG. At this value, there is sufficient pressure drop to provide peak flow through the generator. It is still very much a balancing act between desired SCFM nitrogen output vs. the desired purity of the output.
Contact Us Today Ready to experience the benefits of onsite nitrogen generation for your business? Contact us today to learn more about our advanced solutions and how we can help you achieve your goals.
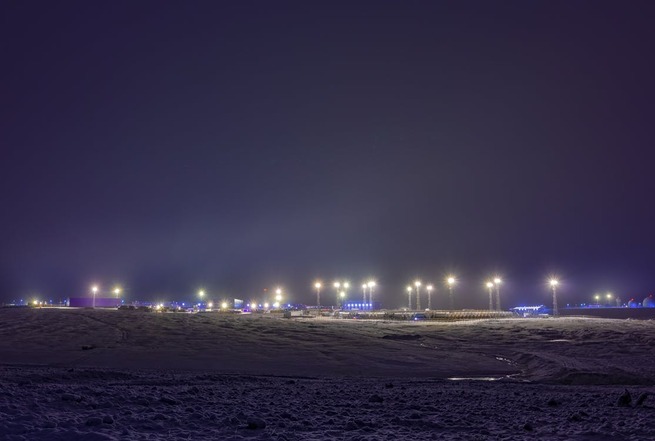
Industrial Manufacturing LED Lighting Upgrades and Controls
Industrial Manufacturing LED Lighting Upgrades and Controls
Introduction
Upgrading to LED lighting in industrial manufacturing facilities is a game-changer for energy efficiency, cost savings, and improved workplace safety. Traditional lighting systems such as metal halide, fluorescent, and high-pressure sodium lamps are energy-intensive, generate excessive heat, and require frequent maintenance. LED technology provides superior illumination, longer lifespan, and significant energy cost reductions, making it a smart investment for modern manufacturing operations.
Benefits of LED Lighting Upgrades in Industrial Facilities
1. Significant Energy Savings
LEDs consume up to 75% less energy than traditional lighting.
Reduced power demand leads to lower utility costs and a smaller carbon footprint.
Advanced control systems, such as motion sensors and dimmers, optimize energy use.
2. Longer Lifespan & Reduced Maintenance Costs
LED fixtures last 50,000 to 100,000 hours, significantly longer than fluorescent and HID lighting.
Fewer replacements mean reduced labor costs and less disruption to operations.
Durable design withstands industrial conditions, including vibration, dust, and extreme temperatures.
3. Improved Workplace Safety & Productivity
High-quality brightness and uniform lighting enhance visibility, reducing workplace accidents.
LEDs provide instant-on lighting, unlike HID lamps that require warm-up time.
Better color rendering (CRI) allows workers to see materials, machinery, and markings more clearly.
4. Sustainability & Compliance Benefits
LED lighting helps facilities meet energy efficiency regulations and green building certifications (e.g., LEED).
Reduced carbon emissions align with corporate sustainability goals.
Mercury-free construction eliminates hazardous waste disposal concerns.
Key Considerations for an LED Lighting Retrofit
1. Facility Assessment & Lighting Needs Analysis
Conduct an energy audit to determine current energy consumption and potential savings.
Evaluate lighting needs for different areas, such as warehouses, production lines, and office spaces.
Consider lumens, color temperature, and beam angles for optimal lighting performance.
2. Selecting the Right LED Fixtures
High-bay LEDs for large open areas with high ceilings.
Linear LED fixtures for production lines and assembly areas.
Task lighting solutions for detailed workstations requiring focused illumination.
Smart LED systems with controls for automation and energy optimization.
3. ROI and Incentives for LED Upgrades
Calculate return on investment (ROI) by comparing energy savings, reduced maintenance, and initial installation costs.
Take advantage of utility rebates, tax incentives, and government programs for energy-efficient upgrades.
Many LED lighting projects see a payback period of 1-3 years, making them financially attractive.
Implementing an LED Lighting Upgrade in Manufacturing Facilities
1. Partnering with an Experienced LED Supplier
Work with an industrial lighting expert to select the best fixtures for your needs.
Ensure compliance with OSHA and industry lighting standards.
Look for warranty-backed products to maximize long-term savings.
2. Professional Installation & Integration
Ensure proper installation to avoid wiring and compatibility issues.
Integrate LED lighting with smart building automation for maximum efficiency.
Schedule installation during low-production hours to minimize disruption.
3. Monitoring & Maintenance Strategies
Use IoT-based lighting controls to monitor energy consumption and adjust brightness levels.
Establish a maintenance schedule to check for dust accumulation and sensor calibration.
Train staff on best practices for using automated lighting systems.
Conclusion
Upgrading to LED lighting in industrial manufacturing facilities delivers substantial energy savings, enhanced safety, lower maintenance costs, and compliance with sustainability goals. By investing in high-performance LED systems, manufacturers can significantly improve operational efficiency while creating a better work environment for employees. With the availability of rebates and incentives, now is the ideal time for industrial facilities to make the switch to LED lighting and unlock long-term cost savings and performance benefits.